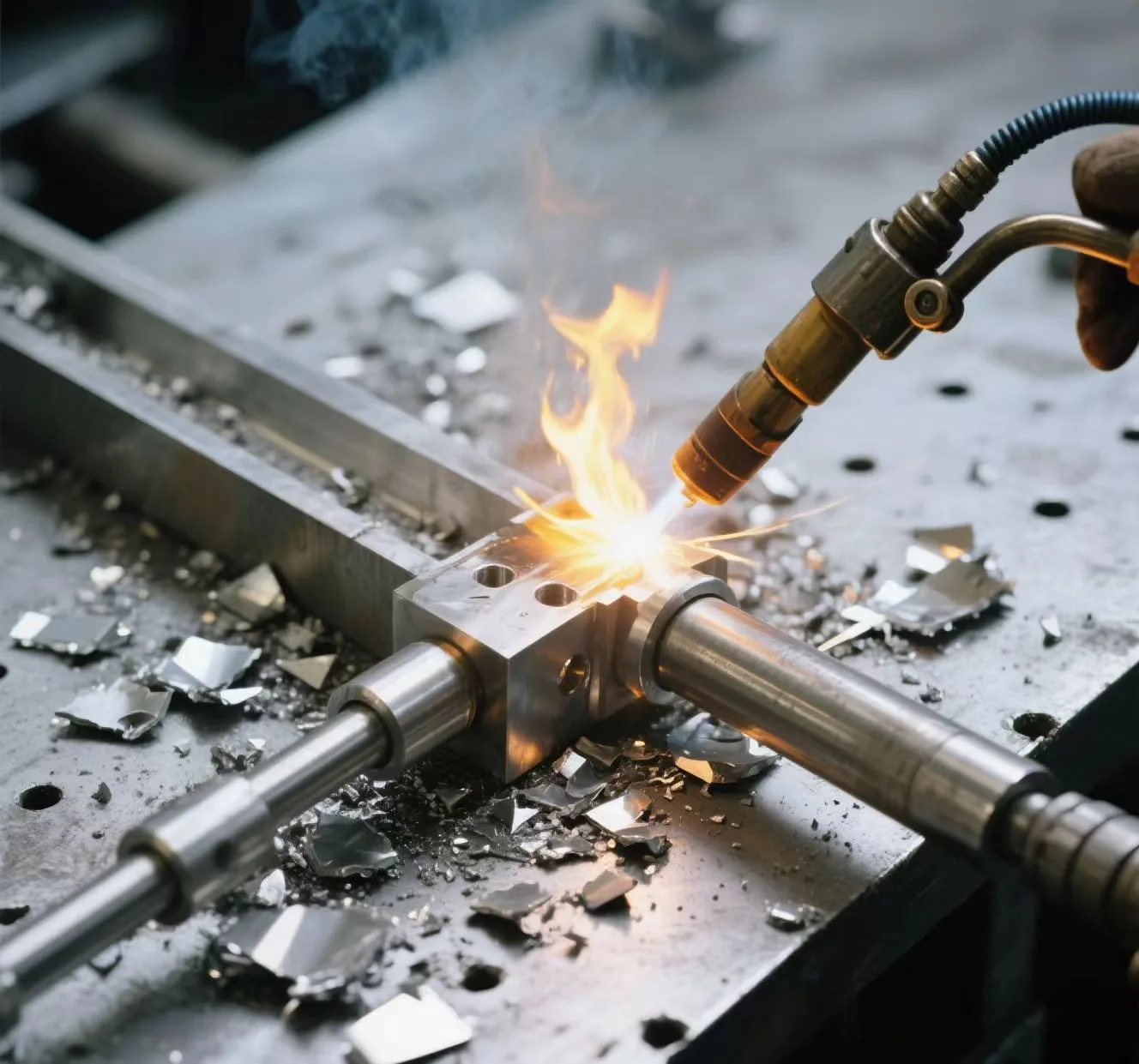
Advanced Techniques for Fabricating the Ultimate Corrosion-Resistant Material
Industry-Proven Welding Methods (And When to Use Them)
Gas Tungsten Arc Welding (GTAW/TIG)
*Your go-to solution for 90% of applications:*
- Quadruple Shielding System:
- Primary argon flow: 25-30 CFH
- Trailing shield: 15-20 CFH
- Backing gas: 20-25 CFH
- Chamber purge: <10 ppm O₂
- Electrode Choice: 2% thoriated tungsten, sharp 30° tip
- Critical Parameter: 1 amp per 0.001″ thickness rule
Electron Beam Welding (EBW)
For mission-critical aerospace/medical components:
- Vacuum level: 10⁻⁴ to 10⁻⁵ torr
- Advantages:
- Near-zero HAZ (0.1-0.5mm)
- 100% depth-to-width ratio
- Zero contamination risk
- Limitations: $500K+ equipment cost
Laser Welding
Precision solution for thin sections (<1mm):
- Fiber/YAG lasers at 1μm wavelength
- Pulse frequency: 50-100 Hz
- Shielding: Helium-argon mixes for improved penetration
The 5 Enemies of Successful Tantalum Welding
- Oxygen Contamination“Visible discoloration = Scrap metal”
- Straw/yellow (400°C): 50 ppm O₂ → 25% embrittlement
- Blue (500°C): 200 ppm O₂ → Full brittleness
- Solution: Real-time oxygen monitors (Teledyne API)
- Heat Management Failures
- Max interpass temp: 150°C
- Cooling rate: >200°C/minute required
- Surface Preparation Sins
- Acceptable: Nitric/HF acid pickling
- Forbidden: Chlorinated solvents, abrasive disks
- Filler Metal PitfallsFiller TypeUse CaseWeaknessERTa1Chemical tanksNb contamination riskTa-2.5WHigh-temp partsReduced ductilityUnalloyed TaUHP systemsPorosity sensitivity
- Post-Weld Stress
- Annealing requirement: 1,200°C for 1hr per inch
- Fixturing must allow thermal expansion
Step-by-Step Welding Protocol (ASME BPVC Section IX Compliant)
Phase 1: Pre-Weld Rituals
- Degrease with acetone (no vapor degreasers!)
- Acid etch: 10% HNO₃ + 2% HF at 50°C
- Brushing: Stainless steel brush dedicated to Ta only
Phase 2: Purge Execution
- Chamber O₂: <10 ppm verified
- Backing gas dew point: <-60°C
- Flow rates: 3x calculated volume displacement
Phase 3: Welding Execution
[PARAMETER CHART] Thickness | Amps | Travel Speed | Gas Flow ----------|------|--------------|--------- 0.5mm | 35A | 12 ipm | 40 CFH 3mm | 120A | 8 ipm | 60 CFH 6mm | 220A | 5 ipm | 80 CFH
Phase 4: Validation
- Dye penetrant testing (ASTM E165)
- Bend testing: 3T radius requirement
- Metallography: Grain structure analysis
When Welding Shouldn’t Be Your First Choice
Mechanical Joining Alternatives
- Explosive bonding for clad vessels
- Tantalum-lined flanges (ASME B16.5)
- Conical seal compression fittings
Emerging Solutions
- Friction Stir Welding: Promising for <6mm sheets
- Cold Metal Transfer (CMT): Low-spatter option
- Diffusion Bonding: For nuclear applications
The Reality for Fabricators
While boutique shops like ATI Metals or Plansee routinely weld tantalum, the $500/sq ft cost reflects its difficulty. For critical systems like semiconductor CVD chambers or pharmaceutical reactors, proper welding isn’t an option – it’s the only option. As TWI Global confirms, “Tantalum welding remains a specialty art where 99% purity isn’t good enough.”