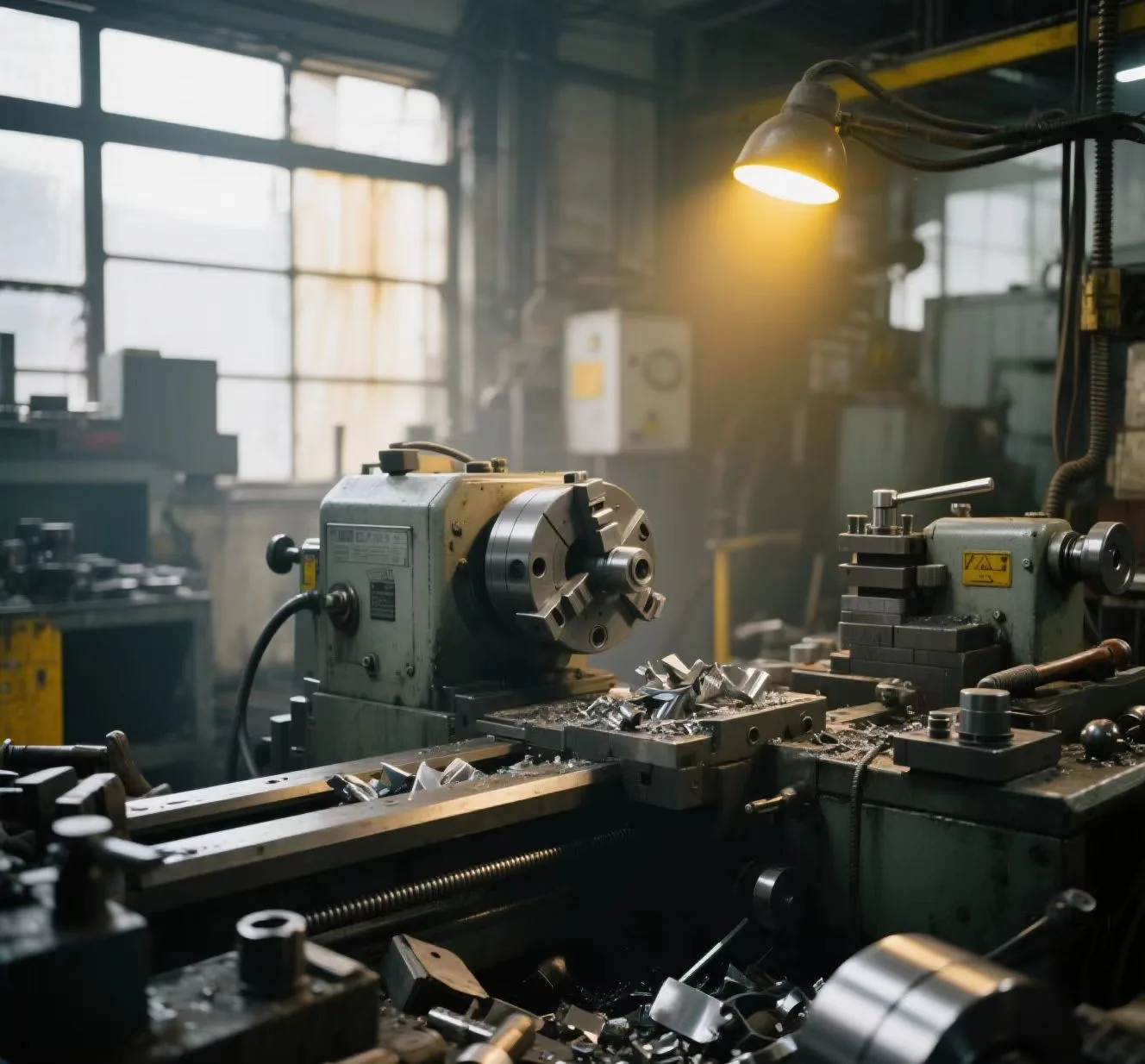
Mining the Source – Your First Encounter With Raw Tantalum
Your journey begins in mines where tantalum ore hides as dense black sands called coltan (columbite-tantalite). This is where you confront tantalum in its rawest form.
Crushing and Concentrating the Ore
Your raw coltan enters processing plants where:
- Crushing: Jaw crushers reduce rocks to 10mm granules
- Grinding: Ball mills pulverize ore into 0.1mm powder
- Gravity Separation: Shaking tables/spirals exploit density differences (tantalum is 2x heavier than quartz)
- Magnetic Separation: Discards magnetic minerals like columbite
Result: 30% Ta₂O₅ concentrate – still far from pure.
The Chemical Leap: Extracting Tantalum Oxide
Hydrometallurgy becomes your tool to isolate tantalum:
- Acid Digestion: Concentrate + HF/H₂SO₄ at 90°C → dissolves Ta/Nb
- Solvent Extraction: Organic solvents like MIBK selectively grab tantalum from the acidic soup
- Precipitation: Adding KCl creates potassium tantalum fluoride (K₂TaF₇) – the “white gold” intermediate
Fun fact: 1 ton of ore yields just 0.25kg of K₂TaF₇ (USGS Source).
Reduction to Metallic Tantalum
You transform salts into metal through two industrial-scale methods:
1. Sodium Reduction (Cheaper)
markdown
K₂TaF₇ + 5Na → Ta + 2KF + 5NaF
- Heated to 800°C in argon atmosphere
- Produces “tantalum powder” for capacitors
2. Electrolytic Reduction (Purer) - Molten K₂TaF₇ electrolyte at 900°C
- Graphite anode/steel cathode apply 7V
- Forms dendritic crystals (99.95% pure)
Refining and Consolidating the Metal
Your powder isn’t ready until it survives these trials:
- Vacuum Arc Melting: Removes trapped gases at 10⁻⁴ torr
- Electron Beam Melting: Zaps impurities at 3,500°C → 99.999% pure ingots
- Powder Metallurgy: For capacitor anodes:
- Press powder into pellets
- Sinter at 1,500°C (creates porous structure)
- Anodize to form dielectric oxide layer
Shaping Tantalum for Critical Applications
You transform ingots into lifesaving tech:
Product | Process | Your Daily Use |
---|---|---|
Capacitors | Powder sintering | Smartphone/computer |
Medical Wire | Cold drawing | Surgical implants |
Corrosion Parts | CNC machining | Chemical reactors |
Sputtering Targets | Hot isostatic pressing | Semiconductor chips |
The Recycling Revolution: Your Urban Mine
Discarded electronics hold 7x more concentrated tantalum than virgin ore. Modern recyclers:
- Shred circuit boards
- Incinerate organics
- Leach metals with HCl/HNO₃
- Separate Ta via solvent extraction
Leading players like Umicore recover 40% of industrial tantalum scrap – a figure you can boost by recycling devices.
Why Processing Matters to You
Every smartphone capacitor represents:
✅ 12 hours of artisanal mining
✅ 3 chemical processing stages
✅ 2 high-energy melting operations
Ethical processing isn’t just industrial – it’s personal. Demand certified conflict-free tantalum through initiatives like iTSCi.