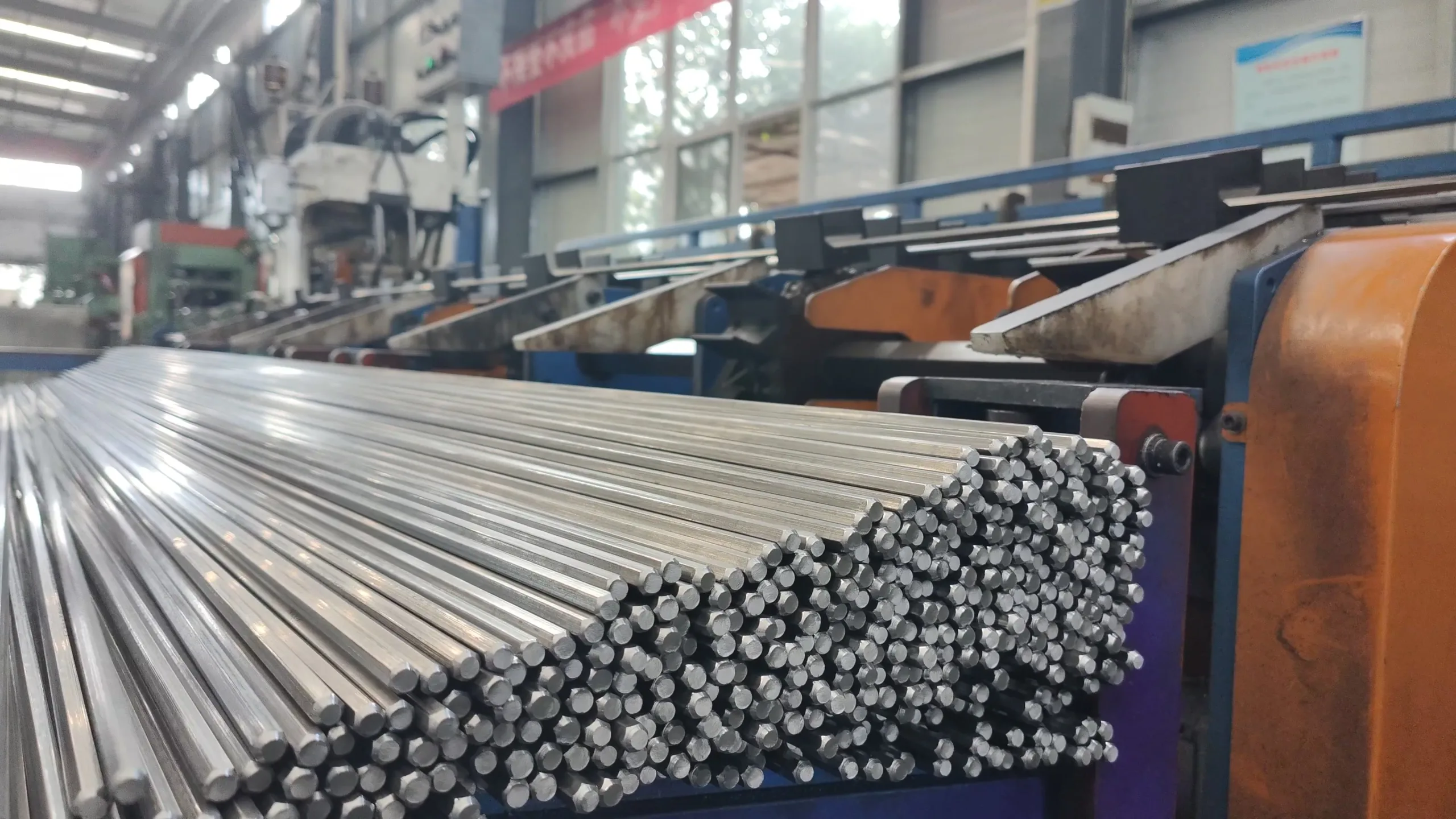
Precision Techniques and Expert Strategies for Machinists
The Short Answer: Yes – With Specialized Approaches
You can machine tantalum successfully, but it demands careful planning and tooling adjustments. Unlike aluminum or steel, this reactive, dense (16.6 g/cm³), and ductile metal presents unique challenges that require tailored solutions.
Why Tantalum Tests Your Machining Skills
Four critical properties impacting your process:
1. Work Hardening Nightmare
- Rapidly hardens during deformation
- Causes tool deflection and poor surface finish
- Solution: Maintain aggressive, continuous cuts
2. Galling Tendency
- Cold-welds to cutting tools
- Creates built-up edge (BUE) and tool failure
- Solution: Specialized coatings and lubricants
3. Heat Sensitivity
- Oxidizes above 300°C → embrittlement
- Discoloration indicates material compromise
- Solution: High-pressure coolant flood
4. Reactive Nature
- Forms pyrophoric chips at high temperatures
- Requires strict dust control measures
Proven Machining Methods & Parameters
Turning Tantalum (Lathe Work)
Parameter | Recommended Setting |
---|---|
Cutting Speed | 30-50 SFM |
Feed Rate | 0.05-0.1 mm/rev |
Depth of Cut | 0.5-2 mm |
Tool Geometry | 15° positive rake |
Insert Material | Micrograin carbide (Tungaloy) |
Milling Tantalum
- Tool Type: 4-6 flute end mills
- Strategy: Trochoidal toolpaths
- Coolant: Sulfur-chlorinated oil (10:1 ratio)
- Critical Tip: Never pause during cut
Drilling Holes
- Peck Drilling: 0.5xD peck depth
- Point Angle: 118°-135°
- Chip Breakers: Essential for swarf control
Conquering 4 Critical Machining Challenges
1. Taming Work Hardening
- Use sharp tools with polished flutes
- Maintain minimum 0.05mm chip load
- Avoid tool rubbing at all costs
2. Preventing Galling
- Tool Coatings: TiAlN or diamond-like carbon (DLC)
- Lubricants: High-sulfur EP additives
- Geometry: Large clearance angles (>10°)
3. Heat Management
- Coolant Pressure: 1000+ PSI through-tool
- Thermal Monitoring: IR sensors on workpiece
- Speed Limitation: Max 150 SFM for roughing
4. Chip Control & Safety
- Chip Breakers: Mechanical notchers
- Dust Collection: HEPA filtration systems
- Fire Prevention: Class D extinguishers nearby
Best Practices for Successful Machining
Tool Selection Guide
Operation | Recommended Tool |
---|---|
Rough Turning | CNMG 432 with TiAlN coat |
Finish Milling | 6-flute carbide end mill |
Drilling | Parabolic drill with DLC |
Workholding Tips
- Use soft jaws with copper lining
- Apply low-stress clamping (<200 PSI)
- Support long parts every 4xD
Post-Machining Handling
- Deburring: Vibratory finishing (ceramic media)
- Cleaning: Alkaline solution bath
- Passivation: 30% nitric acid dip
When to Consider Alternatives
Non-Machining Options
- Waterjet Cutting: For profiles >50mm thick
- EDM: Complex geometries (±0.005mm tolerance)
- Laser Cutting: Thin sheets (<3mm)
Professional Services
For critical components, partner with specialists: