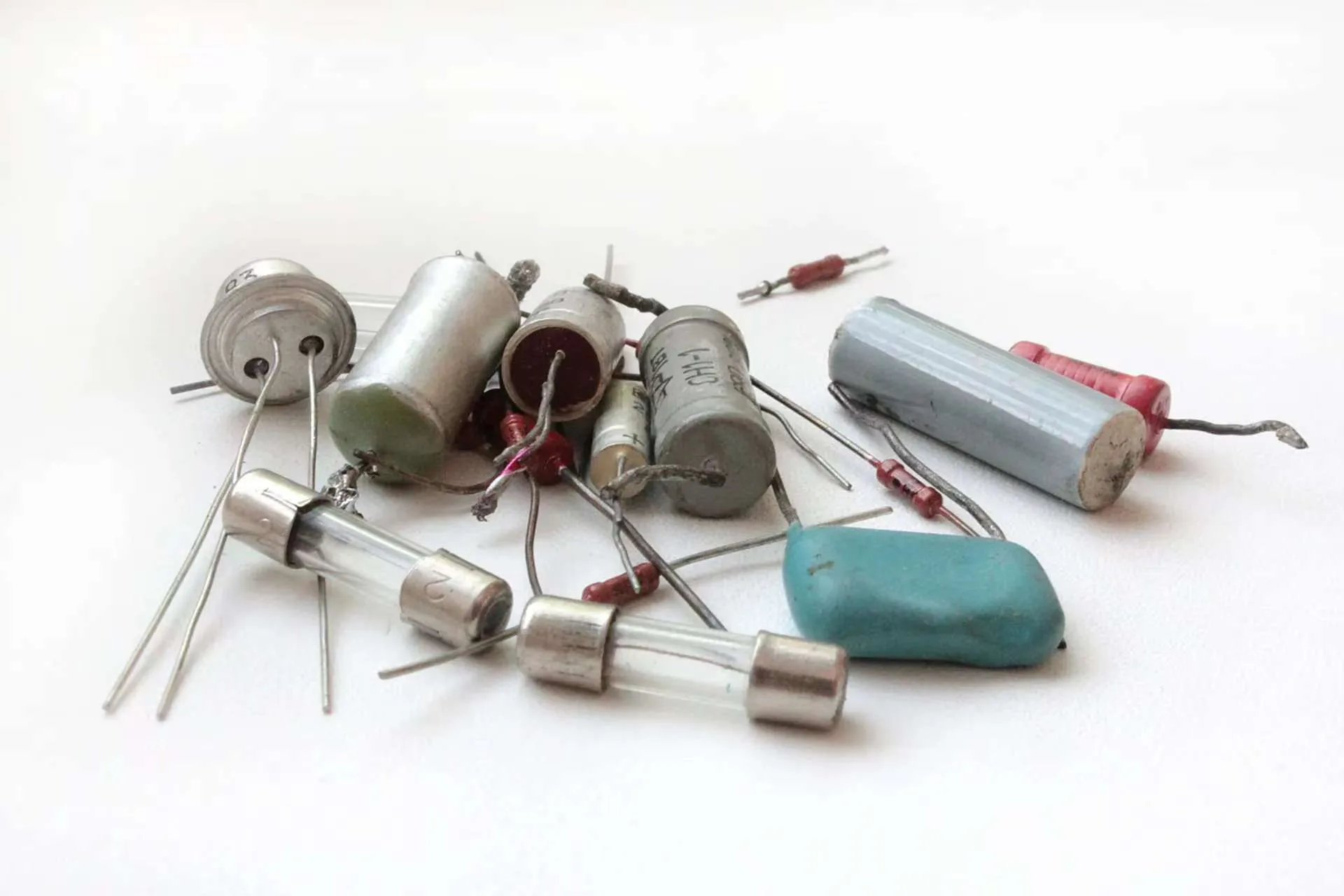
From Raw Tantalum to High-Performance Components – A Step-by-Step Guide
Introduction: Why Tantalum Capacitors Matter in Your Devices
Tantalum capacitors power everything from your smartphone to medical implants, offering unmatched energy density and stability. But how are these tiny, high-performance components manufactured? Let’s break down the intricate process.
Step 1 – From Ore to Powder: Producing High-Purity Tantalum
Mining and Refining Raw Tantalum
- Tantalum is extracted from coltan ore (columbite-tantalite).
- Refined into tantalum pentoxide (Ta₂O₅) via chemical processing.
- Converted to metallic tantalum powder through sodium/electrolysis reduction.
Controlling Powder Properties
- Particle size: 5-20 microns (affects capacitance).
- Purity: 99.95%+ for reliable performance.
- Manufacturers: Leading suppliers like KEMET (KEMET Tantalum Powder) optimize powder for capacitor use.
Step 2 – Forming the Anode: The Heart of the Capacitor
Pressing and Sintering
- Powder is compressed into pellets under high pressure.
- Sintered at 1,500-2,000°C in a vacuum, creating a porous structure.
- Porosity increases surface area, boosting capacitance.
Anodization – Creating the Dielectric Layer
- Pellets are soaked in acidic electrolyte (e.g., phosphoric acid).
- Voltage applied → forms a nanoscale Ta₂O₅ dielectric layer.
- Thickness determines voltage rating (e.g., 50V = ~100nm oxide).
Step 3 – Adding the Cathode: Manganese Dioxide (MnO₂) Coating
Chemical Vapor Deposition (CVD)
- MnO₂ is deposited inside the porous anode.
- Acts as the solid electrolyte, replacing liquid in traditional caps.
Why MnO₂?
- Self-healing: Repairs minor dielectric defects.
- Stability: Performs better under heat/stress vs. polymers.
Step 4 – Assembly and Encapsulation
Lead Attachment & Coating
- Tantalum wire welded to the anode.
- Graphite/silver layer applied for better conductivity.
Molding and Testing
- Encased in epoxy resin (radial) or molded plastic (SMD).
- Rigorous QC checks:
- Capacitance verification
- Leakage current testing
- Burn-in at high temps
Challenges in Tantalum Capacitor Manufacturing
Avoiding “Field Crystallization” (Catastrophic Failure)
- Cause: Flaws in Ta₂O₅ layer → short circuits.
- Solution: Surge testing weaks out defective units.
Ethical Sourcing Concerns
- Conflict-free supply chains required (e.g., iTSCi certification (iTSCi Program).
The Future: Polymer Tantalum Capacitors
- Conductive polymer replaces MnO₂ → lower ESR, higher reliability.
- Used in 5G, EVs, and aerospace (AVX Polymer Tantalum Guide).